The Effectiveness of Polyurethane Wheels in the Hyperloop Pod Competition
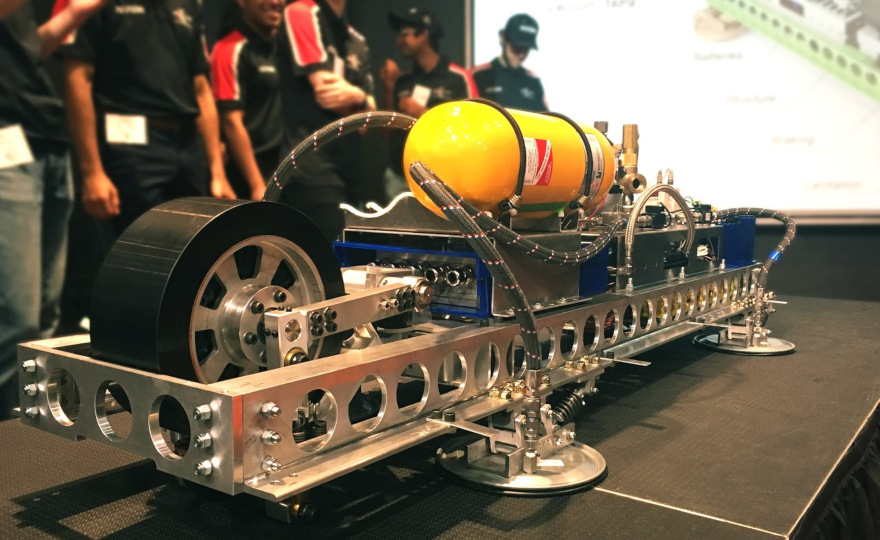
The Process
Our task was to engineer polyurethane drive, stability, and clamping wheels that could hold up to ultra-high speeds. Working alongside the student teams, we assisted in hub design, advised material selection, and produced the final wheels.
Design
Hub Design
Each university team provided us with their proposed hub drawings. Groups aimed to minimize the hub’s weight without sacrificing load and speed requirements. The hub design process was iterative and accounted for manufacturing feasibility and the ability to work within the desired size, acceleration, and radial load constraints.
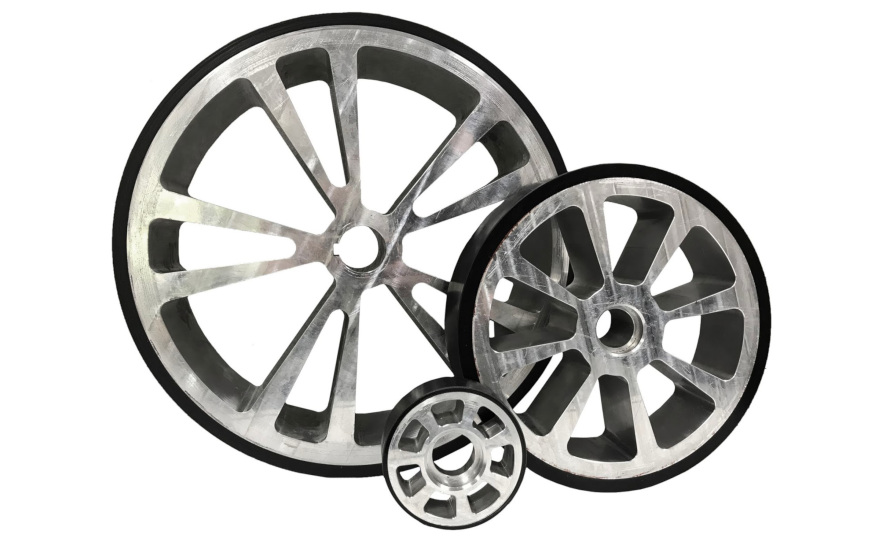
Material Selection
While the hub design is important, the material plays a critical role in the success of the wheel and this is where our expertise counts. Generally speaking, the final material selection is based on the required dynamic properties, abrasion resistance, and compression set. When the teams were expected to reach a top speed of over 200 mph, there were many tradeoffs within the performance of the material to consider.
When it comes to polyurethane, there are tradeoffs in the performance properties among the different material hardnesses. Harder materials generally have a higher tolerance for high loads, speeds and better cut and tear resistance. However, the harder the material, the weaker the traction and braking ability. Our job was to find a middle ground that could endure high speeds requirements while providing a successful, quick deceleration.
To validate the wheels for the specified load and speed requirements we first completed in-house testing and analysis. Most of the wheels we sell today face max speeds of around 8-10 mph and our testing equipment reflects this. To further check our findings, we were able to leverage the extensive data held by our suppliers to ensure we chose the best material for the application at hand.
Testing
Along the way, a combination of internal and external testing methods and research were used to prove that the wheels could stand up to the competition. Internally, we used our dynamometer to test for failure at different loads and speeds. Due to the nature of our existing product range, our dynamometer tests for maximum speeds of 9 mph and up to 4,800 lbs. Our testing gave us some information, but our prepolymer supplier was needed to support the findings with technical data.
Externally, the competing teams used their own forms of dynamometer testing to confirm that the materials were appropriate for their target loads and speeds. For instance, Paradigm ran its front vertical stability wheel on a test stand that could nearly simulate the actual pod run. Each wheel underwent similar tests, and the students then analyzed parts for any failure in the rim, shaft, bearing assemblies, or debonding.
Competition Results
The MIT Hyperloop team relayed specific feedback regarding the success of their wheels. They said the casted propulsion wheel was so well balanced that with above 6500 rpm (72 mph for the drive wheel), no visible/audible vibration was generated. Also, under 4000 N nominal clamping force, the propulsion and clamping wheels did not experience permanent deformation or creeping behavior throughout their 3-month testing and competition period. Also, the stability wheels were able to withstand impulse forces generated by the gap of the track. This team felt the wheels performed exceptionally well.
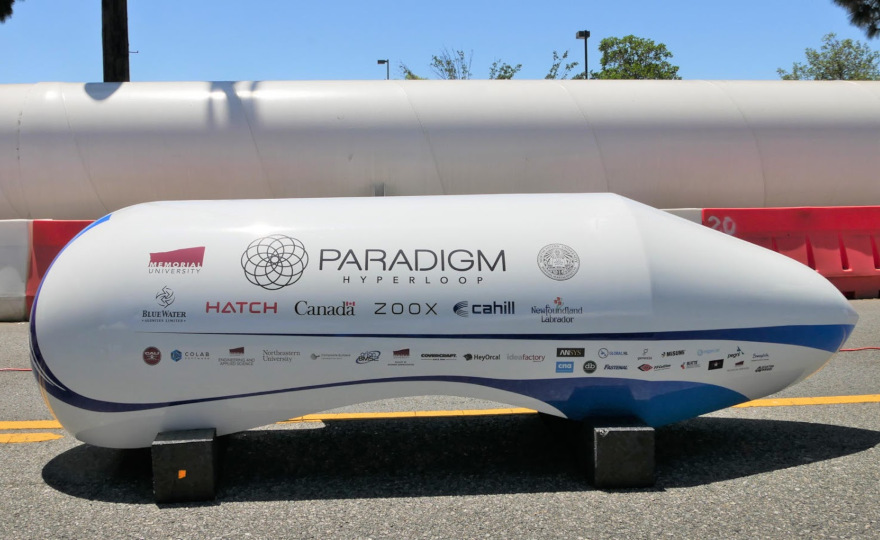
MIT Hyperloop II finished 5th internationally and first in the US. They also took home an innovation award for their design. Paradigm took second place in 2017, and in 2019, the team took 8th overall, ranking 3rd in the US. For more information read the full report: The Effectiveness of Polyurethane Wheels in Proposed High-Speed Transportation.
So what does this mean for other industries?
A vast majority of the wheels and tires we produce are used within the material handling industry on different class forklifts. Still, this competition stresses the point that our polyurethane wheels can excel within a broader range of applications. We received a lot of feedback from the teams we worked with, but three things stood out to us as being universally relevant to the diverse industries we serve. The lack of vibration and deformation in the wheels paired with our advanced manufacturing capabilities make a strong case for the quality of Stellana wheels.
Lack of vibration
Our casted propulsion wheel was so well balanced that with above 6500 rpm, no visible or audible vibration was generated. Depending on the wheel application, vibration can create a significant issue. For example, the wheels used on AGVs and robots should not produce vibration. When looking at robots, things like localization accuracy and encoder odometry could be impacted by bumpy wheels. Perfectly round, smooth-running wheels will limit the error that accumulates with each revolution.
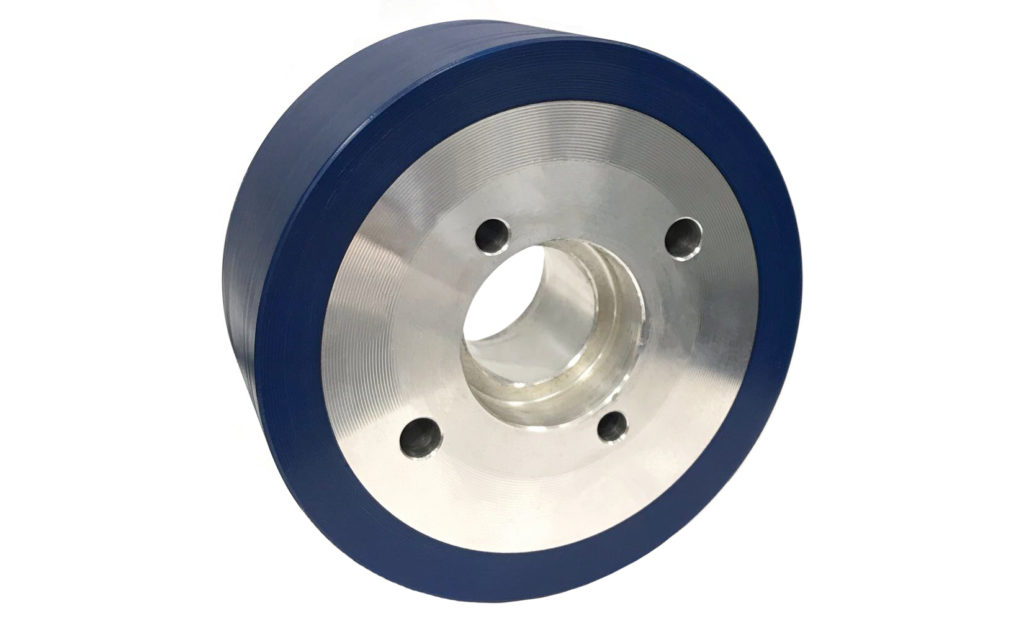
Similarly, the wheels used in metal roll forming machines should be perfectly smooth. At Stellana, we hold our diameters to tight +/- .005 tolerances, ensuring you receive a wheel that is as perfectly round as you can find in the industry. This is one of the most significant differentiating factors between standard polyurethane products and the Stellana-made versions. It results in less hassle and cost associated with machine adjustments, roller failure, and cosmetic issues.
Lack of deformation
In addition to the lack of vibration, the wheels kept their shape. The team reported no sign of distortion or creeping throughout the entire testing and completion periods. If you have heard the term “flat spotting” you may know polyurethane can experience profile irregularities after use. Unwanted flat spots can form in the round tire due to the material overheating during use and then cooling while parked. These spots can also occur from the skidding or “peeling out” of the tires when the traction is not adequate. This is one common way forklift tires experience deformation, which leads to rider discomfort and machine inefficiency.
Manufacturing flexibility
Beyond the performance of the wheels themselves, our machining capabilities allowed us to turn polyurethane to the exact dimensions required. Also, we were able to utilize and modify existing tooling to accommodate different hub designs. The flexibility in our manufacturing process also allowed us to tackle last-minute design changes. Being nimble in this way, we could manufacture new, unique products without high cost or disruption to everyday production.
Pushing the envelope helps us to grow at Stellana. Challenging our products with new extremes and unheard-of applications gives us greater confidence in just how well our products perform. Through these opportunities, we continue to build our reputation as the leading producer of highly engineered polyurethane wheel solutions.
About Stellana
Stellana is the leading global manufacturer of polyurethane, rubber, thermoplastic, and TPU wheels. With more than 60 years of industry experience, we are the material handling industry’s largest global supplier of polymer wheels. Strategically located in Sweden, Germany, the United States, China, and Sri Lanka, we offer a comprehensive range of wheels and tires.