Six Questions to Determine the Polyurethane Tire You Need
When it comes to tires, we can agree that they are round, and they roll. So, selecting the right one should be pretty straightforward, right?
Back in February 2019, we covered the basics of what to consider when selecting the best tire for your needs. We hope this information improved your polyurethane knowledge and confidence in material selection, but we realize the details might slip your mind when you are in the field. For this reason, we created a material selection guide that can be easily used to analyze a facility’s needs and identify the best-suited material. In a technical industry, the idea of chemistry and polymer formation can be intimidating to many of us. We’ve identified six simple questions that get to the bottom of your needs, stripping away the daunting engineering values that can be hard to interpret.
Importance of Material Selection
In most cases, the search for a new material comes as the result of tire failure or the sense that another could deliver more of the qualities desired (comfort, load capacity, etc.). Finding a better material can limit the headaches and costs that are associated with an ineffective one. Tires account for a significant portion of the equipment’s overall maintenance, but the proper material selection will minimize this.
During the selection process, premium materials may be overlooked to avoid higher costs– and in some cases rightfully so. Not every application is demanding enough to benefit from a premium material, but many do. Premium parts often save the end-user money as a result of fewer necessary repairs, service calls, and replacement parts. Experience with failing parts can make it hard to justify a more significant investment in your tires. However, price-driven searches find the cheapest parts that continue to need replacing and increase costs in the long run. It can be hard to justify until you experience the Stellana difference, but investing in the best parts for the equipment’s usage is a huge cost saver over time.
In addition, selecting the right material improves customer relations and satisfaction. Dealers aim to keep their end-users happy, and the OEMs do not want to pollute their brand image with failing parts. Along these same lines, choosing the right tire material will help your equipment perform as it was intended to. Operators can move faster and carry heavier loads which increases operational efficiencies. In one instance, a customer of ours was able to remove the speed constraints previously programmed into their trucks in an attempt to correct poor tire performance before using Stellana drive tires. Don’t limit the effectiveness of your equipment with low-value wheels. Make sure you get the most picks per hour from your tires because that alone will justify the cost.
Tire Material Selection Guide
When looking at Stellana tires, it is easy to see the color differences among our materials, but it is not as easy to understand what differentiates them. This guide was intended to steer you in the right direction and encourage you to ask the questions that are the most significant deciding factors in material selection. The equipment will dictate the tire’s required size and dimensions. It is the material that is open to more interpretation.
There are a lot of technical data sets to sift throughout your selection process, so we boiled it down to six questions that capture the significance of the figures. We even did it in a way that your coworkers outside of the engineering department can use and interpret to make informed decisions.
Here are the six main things to consider:
- What are your load requirements?
- What are your speed requirements?
- Is there a presence of moisture in your environment?
- How would you describe the flooring quality?
- What is the temperature in your facility?
- Are there any harsh substances present (such as oil or chemicals)?

One other consideration worth noting is the run length. It can be more difficult to quantify this metric directly but taking into account the distance between picks is important. In some applications, trucks are moving just 100 ft between picks whereas some travel thousands of feet between picks. Similarly, in many of today’s large facilities, trucks run continuously as opposed to intermittently. The longer the run, the more heat build-up a tire incurs. Harder materials tolerate heat better, as a general rule, due to the reduced compression in the material.
Interpreting Your Results
By answering these questions, you’ll identify a material that will work for you and there may even be a few. Once you fill out the guide, you will notice that there is some overlap between the materials that will potentially work for your application.
The main contributor to this overlap is the material’s durometer. We have two 90A durometer materials – the Smoothy 90 and the max90. The Smoothy™ tire is the same hardness as the max90 and offers the same speed and load performance, but they are not the same. The Smoothy is made using zero total indicator run-out (TIR) technology. Meaning our engineering and manufacturing processes provide uniformity in roundness that is maintained even after being pressed onto the hub. This perfect roundness offers a smoother, safer, and a more energy-efficient ride that is better designed to tackle the increasing heights and accuracy requirements within reach truck and picker applications in comparison to the max90.
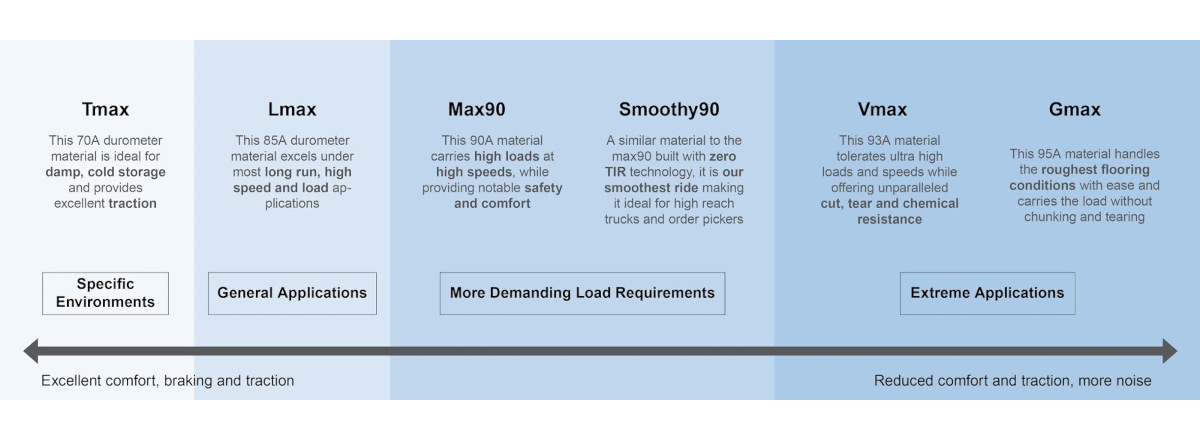
Other Applications
We designed this guide as a resource for forklift tire selection, but we produce wheels and tires for many different uses. Our material expertise can contribute to any stage of the material selection process within any industry. Polyurethane is a versatile, durable material that produces excellent solutions through proper material selection, design, and manufacturing. If you have an application, you would like to investigate further, please contact us at info@stellana.com to begin working with a polyurethane expert.